Pressure Sensors for Liquid Level
Be informed with the most recent developments, articles and news about our company & products.
Filter by Category
Ex-stock Products
Informative Articles
Recent News & Events
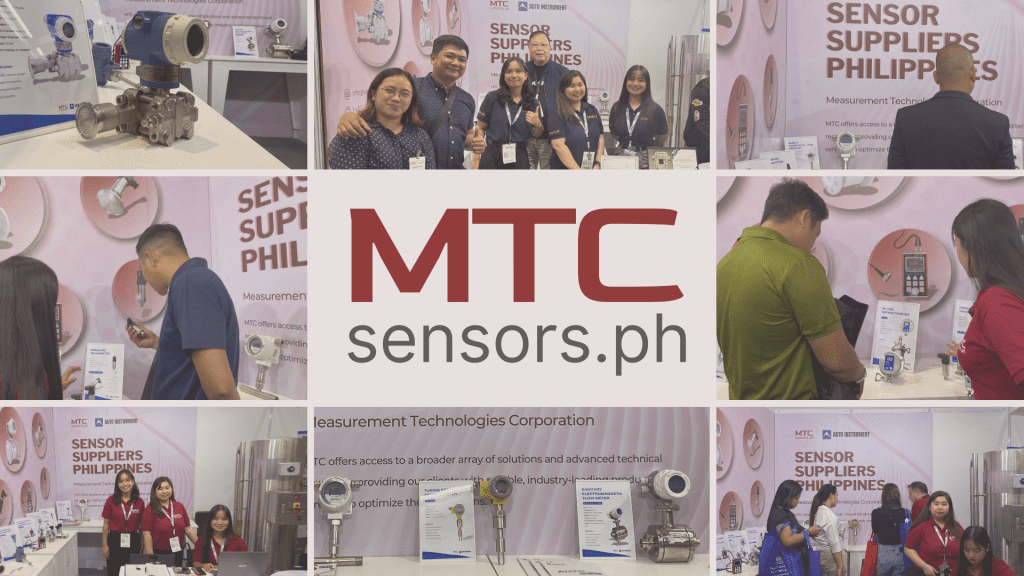
ProPak Philippines 2025
February 12-15, 2025
Measurement Technologies Corporation at ProPak Philippines 2025 – Metro Manila, Philippines
Liquid Level Measurements Using Pressure Sensors in the Manufacturing Industry
Importance of Cost Savings
In the manufacturing industry, prioritizing cost savings is crucial for both smaller and larger companies undertaking projects without the burden of overpriced instruments. Utilizing pressure sensors, a traditional yet effective method involves measuring liquid levels in a tank by assessing the water column. Even for non-water liquids, these sensors prove effective when an intelligent correction factor for density and liquid type is applied.
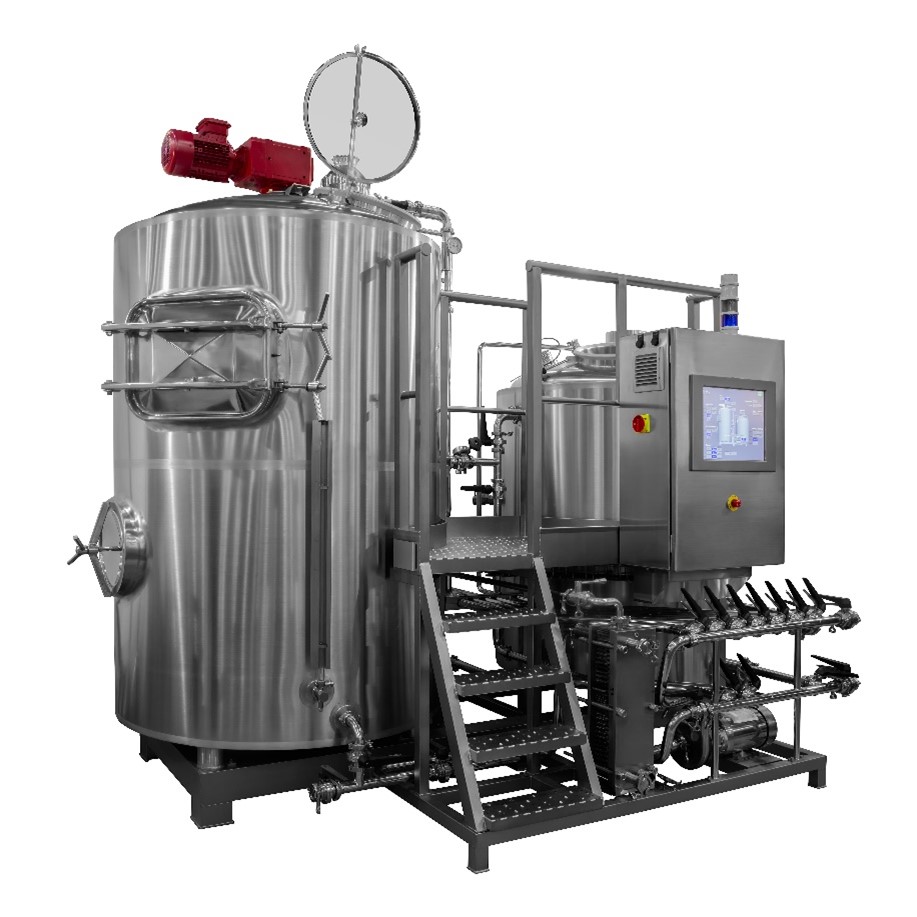
Configuration for Efficient Level Indication
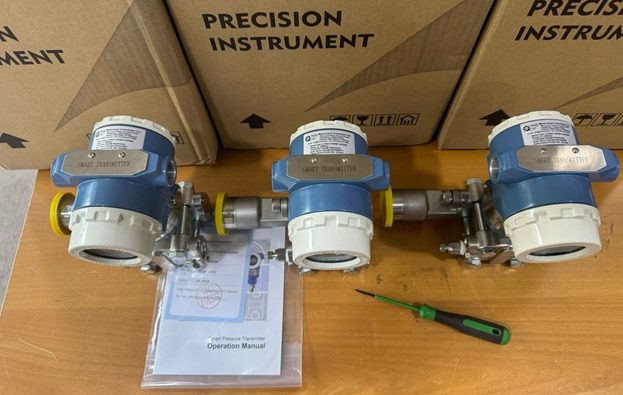
Our team has successfully configured pressure sensors for level indication in the Philippines, offering significant savings in both cost and time for tank fabricators. These reliable level measurement devices help prevent overspill, empty tanks, and ensure basic control of the final liquid product.
User Familiarity and Installation Points
Once users acquaint themselves with pressure sensors for level measurement, selecting the appropriate installation point for the sensor becomes a straightforward process.
Revisiting Traditional Methods
Amidst the influx of newer technologies, it’s essential to remember the reliability of traditional methods. Measuring pressure exerted by a volume of liquid at the tank or well’s bottom proves sufficient, especially for non-critical applications. Standard pressure sensors can be converted into level-based transmitters by considering factors such as tank type, size, and liquid specific gravity.
Enhancing Compatibility & Versatile Connection Options
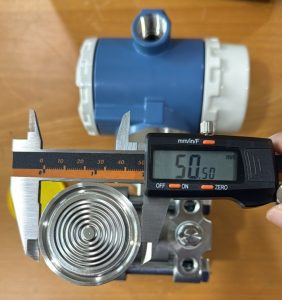
Correctly specified connections pose no issues, whether installing in NPT, BSP, or sanitary type connections using a Tri-Clamp.
In all technologies, there are advantages and disadvantages. However, using pressure-based level sensors correctly minimizes issues like foam build-up, vapors, and physical objects in the tank. This is because we are measuring “pressure,” directly correlated to a level measurement using a calibration method for zero and span.
In the case of pressurized tanks, the level sensor remains an option but requires careful consideration, as it might be necessary to measure the differential pressure from certain points.
Having trouble selecting the best instrument for your application?
Here’s a guide to help you choose the right instrument for your industry. You may also reach out to our technical team for expert guidance tailored to your specific process needs.
Available Product
Other Related Topics
Measuring how far an indentor will penetrate into the material.
Continuously measure a liquid flowing through a pipe or inside a tank
Precise measurement of liquid levels in tanks across industrial and commercial settings
EESiflo system has significantly improved the quality control of the chocolate produced at the factory.
Instrument that senses a mechanical pressure and either displays this pressure, transits this pressure to another location
Designed to accurately measure the moisture content in cement and related materials during production.
Measure water quality online with specific input parameters such as pH, ORP, and Conductivity
A level sensor can also be implemented for use as a level switch.